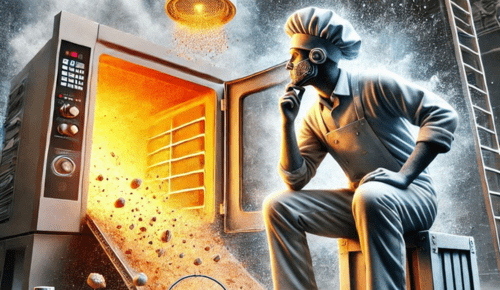
A powder coating oven is a finely tuned system where precision meets efficiency to deliver flawless finishes. But what happens when powder residue starts to accumulate inside? This seemingly minor issue can snowball into a series of complications that quietly drain performance and quality. Understanding how powder build-up impacts your oven’s operation can save time, energy, and costly repairs.
Disrupting Heat Flow Dynamics and Leading to Uneven Curing Outcomes
Powder build-up might not seem like a big deal at first glance, but even a small accumulation can disrupt the delicate balance of heat flow inside the oven. Reliable powder coating ovens depend on consistent heat distribution to ensure every surface cures evenly. When residue obstructs air ducts or settles on heating elements, it creates temperature disparities.
These uneven heat zones can lead to coatings that are over-cured in some areas and under-cured in others. Not only does this compromise the visual appeal of the finish, but it also weakens its durability. Over time, you might notice chips or peeling, which could have been avoided by addressing powder residue early on.
Keeping your powder coating oven clean ensures uniform heat flow, giving every piece an equal shot at a flawless cure. Regular cleaning schedules can prevent small disruptions from spiraling into bigger problems.
Increasing Energy Consumption As the System Compensates for Blockages
When powder residue builds up in the oven, it’s not just the coating quality that suffers—your energy bills do too. Quality powder coating ovens are designed to operate at peak efficiency, but blockages force the system to work harder to maintain the required temperature. Fans may spin faster, heaters might stay on longer, and overall energy use climbs.
This increased energy consumption doesn’t just hit your wallet; it also shortens the lifespan of oven components. Motors and heaters under constant strain are more prone to failures and require replacements sooner. Addressing powder build-up proactively keeps your system efficient and reduces the risk of unexpected breakdowns.
An energy-efficient powder coating oven isn’t just good for the environment—it’s good for your bottom line. Regular inspections and cleaning help you avoid energy waste caused by residue buildup.
Compromising Airflow Efficiency and Coating Consistency Across Surfaces
Airflow plays a critical role in powder coating ovens, ensuring every part of the piece receives consistent heat exposure. When powder accumulates in areas like exhaust systems or vent openings, airflow becomes restricted. This leads to uneven air distribution, which directly impacts the consistency of the coating.
For instance, a piece placed near a blocked vent might receive less airflow, causing insufficient curing. Meanwhile, another piece closer to a working vent could be overexposed. This inconsistency translates to quality control issues and can lead to rework, adding time and cost to the production process.
Ensuring your powder coating oven maintains optimal airflow efficiency is vital for reliable results. Taking the time to inspect and clean air channels ensures that every piece in your batch gets the same quality treatment.
Accelerating Wear and Tear on Oven Components Due to Thermal Strain
Powder build-up doesn’t just affect airflow and heat—it can also increase the strain on the oven itself. When residue collects on heating elements or in exhaust systems, it creates hot spots that lead to thermal stress. Over time, this can cause cracking, warping, or other damage to critical components.
Reliable powder coating ovens are built to last, but excessive strain can wear them down prematurely. Replacing or repairing oven parts isn’t just expensive—it can also bring your operations to a grinding halt. Avoiding these issues starts with a proactive approach to cleaning and maintenance.
Protecting your investment in a quality powder coating oven means staying ahead of wear and tear. Regular cleaning keeps your oven running smoothly and extends its lifespan, saving you from costly downtime.
Elevating Contamination Risks That Degrade Coating Quality over Time
Powder build-up isn’t just a mechanical issue—it can also lead to contamination that impacts the quality of your coatings. Residue inside the oven can flake off or become airborne during operation, settling on freshly coated parts. These contaminants can cause imperfections like bubbles, streaks, or uneven finishes.
In industries where aesthetics and durability are critical, such defects can lead to rejected products and lost revenue. Compact powder coating ovens are designed for precision, but they need to stay clean to deliver on their promise of quality. Addressing powder residue ensures that every piece you produce meets high standards.
Keeping your powder coating oven free of contaminants isn’t just about cleaning—it’s about safeguarding the reputation of your work. A clean oven equals consistent results, every time.
Requiring Frequent Maintenance Interruptions That Reduce Overall Productivity
When powder build-up goes unchecked, it eventually leads to larger problems that require more frequent maintenance interruptions. These unplanned stops disrupt workflows, delay projects, and reduce productivity. What might have been a quick cleaning task can snowball into a full-scale repair job.
A well-maintained powder coating oven operates smoothly, allowing you to meet deadlines and maintain customer satisfaction. By addressing residue regularly, you minimize the risk of downtime and keep your operations running like clockwork.
Compact powder coating ovens are known for their efficiency, but they rely on regular upkeep to stay that way. Investing time in preventive maintenance keeps your projects on schedule and your customers happy.